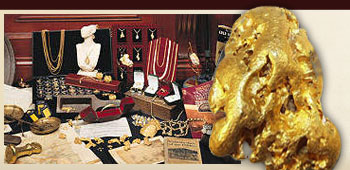
of Gold gifts, Jewellery and Souvenirs
8a Lydiard St North, Ballarat, Victoria, Australia
Telephone/Facsimile: +61 3 5333 4242
Email: mail@thegoldshop.com.au
>> view cart
Friday 22nd Aug, 6:05am
The Gold Shop Globe
So you have seen the image of the gold nugget globe that I (Cordell Kent) made using a state of the art LaserStar welder. This globe was made as a test of the ability of the Laser welder to work with a difficult medium, to make a difficult shape, using space age technology. The effect is nothing short of stunning. Most people look at the nugget globe and see a roughly round shape, made from natural gold nuggets. Few people think about how difficult this was to make, and the technology that was used to make it (more on the Golden Globe later).
After more than 5 years of research into Laser technology for micro welding I made the decision to invest in the high tech laser technology to solve a problem. As a manufacture of natural gold nugget jewellery, with a world wide reputation, the pressure was on to be innovative, and the technology of the laser welder has created new opportunities with small gold nuggets.
Never afraid of embracing new technologies, my Ballarat based company, Australian Native Gold Pty Ltd was the first company in the world to create a dedicated web site for supplying gold nuggets and gold nugget jewellery to the world. This was done with Mr George Fong’s (IT Web Guru) assistance in about 1993. At the time gold nuggets were being found in abundance in all sizes, but over the past few years the quantity of natural nuggets being found has decreased, as has the average size of the nuggets being found. I looked for an innovative method to work with very small natural gold nuggets to manufacture high quality nugget jewellery. Traditional ‘torch and solder’ jewellery manufacture techniques have limitations that make close proximity, high strength, ‘clean’ joins extremely difficult. A different manufacturing method was needed. Laser welders have been introduced into the market place as a specialist manufacturing tool for micro welding a vast range of metals. The laser manufactures have made their products to fill a gap in the jewellery, spectacle frame, dentistry and other specialist markets, for manufacture and repairs. Laser welders are used for manufacture and repair of titanium and stainless steel spectacle frames, dental bridge repairs, and for creating metal joins of similar and dissimilar metals.
The laser welder I have can fire a single, or multiple burst of controlled laser ‘shots’ to an impact area from 0.2mm to 2mm. Control of the laser beam includes pulse duration, pulse wave shape, pulse frequency and voltage. All work is done within a specially designed work chamber in the laser unit. This unit has multiple levels of safety levels integrated into it including hand sensors, door sensors, and light frequency specific filters to block out any chance of the laser beam causing injury or damage outside the work chamber. The laser user looks through a set of Leica binocular microscope with a 15X magnification. A distinct, but ultra fine crosshair positions where the laser beam will hit. The focal length of the eyepiece is tuned to the laser, so if the object is in focus, the beam will be focused and most powerful. To ‘fire’ the laser a foot control is used. The laser beam creates a round impact area, instantly melting, and joining the metals of the join. Multiple overlapping joins will create either a liner or desired weld area. If required the item being joined can be placed on an angle to the laser beam so the strike area smooths off the surface by shooting along the top of the joined surfaces.
If required, the controls of the Laser can be turned up and the laser welder, becomes a laser drill, and an ultra fine hole can be ‘burnt’ through about 4mm of solid metal. The different metals that the laser can be used on include, all Karats (carats) of gold, titanium, platinum group metals, stainless steel, sterling silver, ‘pot’ metal and many more.
Using a filler wire, the laser join can be built up, or in the case of a wear point on contacts, or gem stone settings the laser and filler wire can build up the worn point to original height and shape. One of the features of the laser welder for jewellery and other repairs, the impact point of the laser can be controlled and selected so work on metal can be done in close proximity to heat sensitive objects, such as precious gem stones. This eliminates the requirement of removing a precious stone from a setting to build up one claw.
This application has wider use. For example the laser can repair broken spring stainless steel (battery) clips without taking the temper off the spring, while at the same time making an extremely strong join.
Back to the Golden Globe please consider this. Each nugget had to be individually chosen for the place it was going to be ‘set’ into. Each nugget had to be aesthetically sympathetic and complementary to each nugget around it. Each nugget is joined in at least 3 places to nuggets surrounding it. Each final join or weld, took between 3 and 8 laser shots.
Each join required me to be able to place the crosshairs on the impact area, each ‘shot’ required calculations of which voltage, beam duration, pulse form, and angle of incidence to be used. As only natural gold nuggets were used, each one is unique. For a manufacturer this means each nugget had a different thickness that was not similar to the shape of the nugget adjoining it, so every join had to be carefully considered and calculated. Most joins are invisible to the naked eye. To maintain my requirement to have the Golden Globe 100% Australian Native Gold, some filler wire was required, and natural gold nuggets were melted down, and drawn out to extremely fine native gold wire (no alloys) and this was used with the laser to create ‘strengthening’ bridges and joins. I chose to make a nugget Golden Globe as he felt it was the most difficult of shapes to make, from small relatively flat but uneven shapes, of different sizes and profiles. The effect is stunning.
Although the finished product look relatively ‘simple’ the process was complex and blended 400 million year old natural gold nuggets with space age technology to create a work of art that used technology in an innovative manner.
Laser welders are not inexpensive, and not many small businesses can justify the cost of this form of technology. The Mining Exchange Gold Shop sees the adoption of technology in an innovative manner as a way of opening new frontiers. Already a whole new range of gold nugget jewellery has been designed and made. The most difficult thing about supplementing traditional jewellery manufacturing techniques with space age technology is the need to ‘unlimit’ your thinking from old manufacturing limitations, and embracing the concept of new possibilities that now can be accomplished.
I chose to have a video camera mounted inside the weld chamber so the manufacturing process can be hooked up to a TV screen and other people can see what is happening during the welding process. Due to current space constraints, at the moment, the laser is not in The Mining Exchange Gold Shop, but plans are in place to have this machine where the public can see and experience this exciting technology being used.
Feel free to come into The Mining Exchange Gold Shop or keep visiting this web site to see the new range of unique jewellery I am designing and making. I also make pieces on a ‘special order’ basis, so if you have a design in mind float it past me and we can talk about creating something wonderful.